Lightsaber Hilt
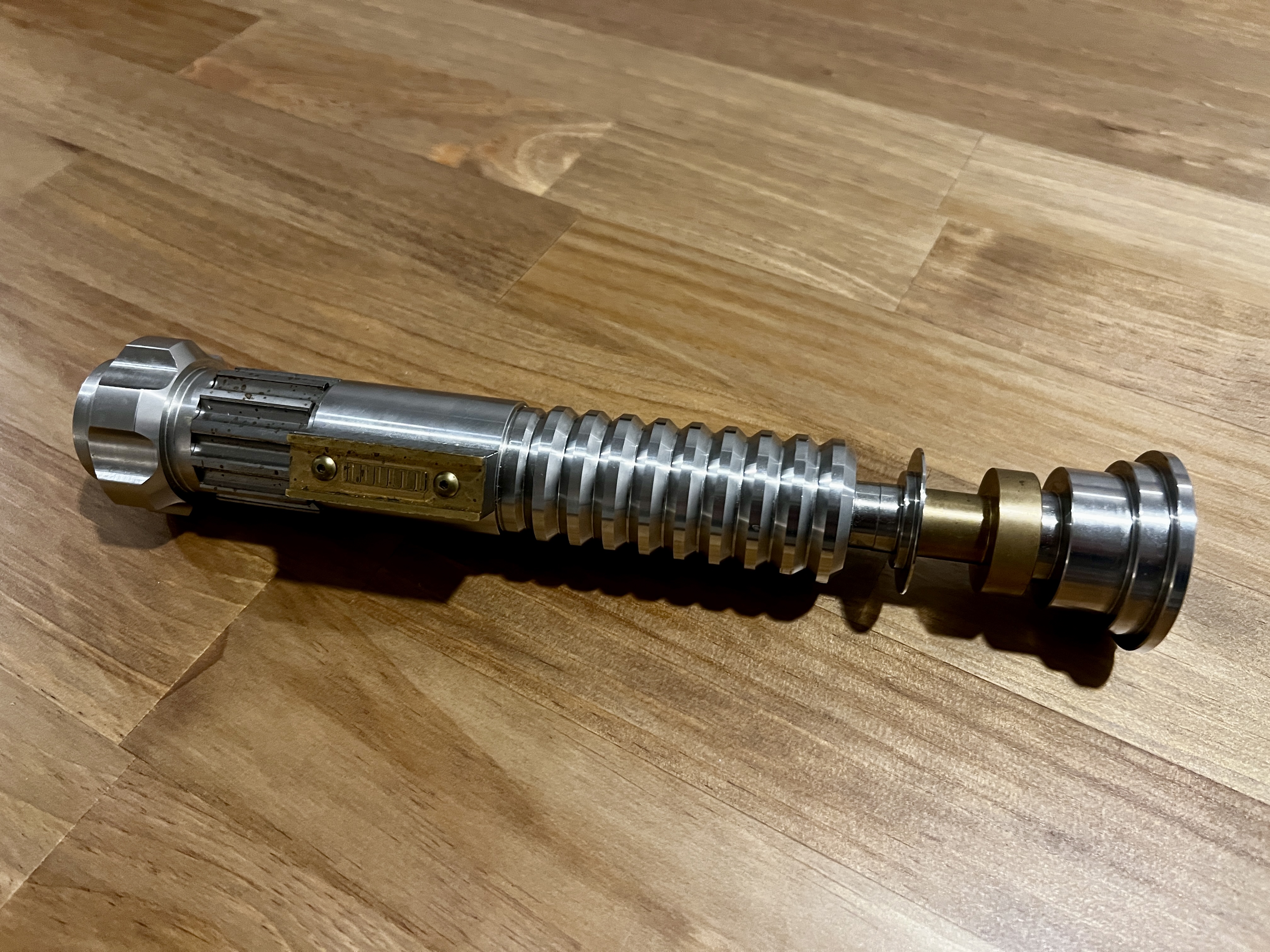
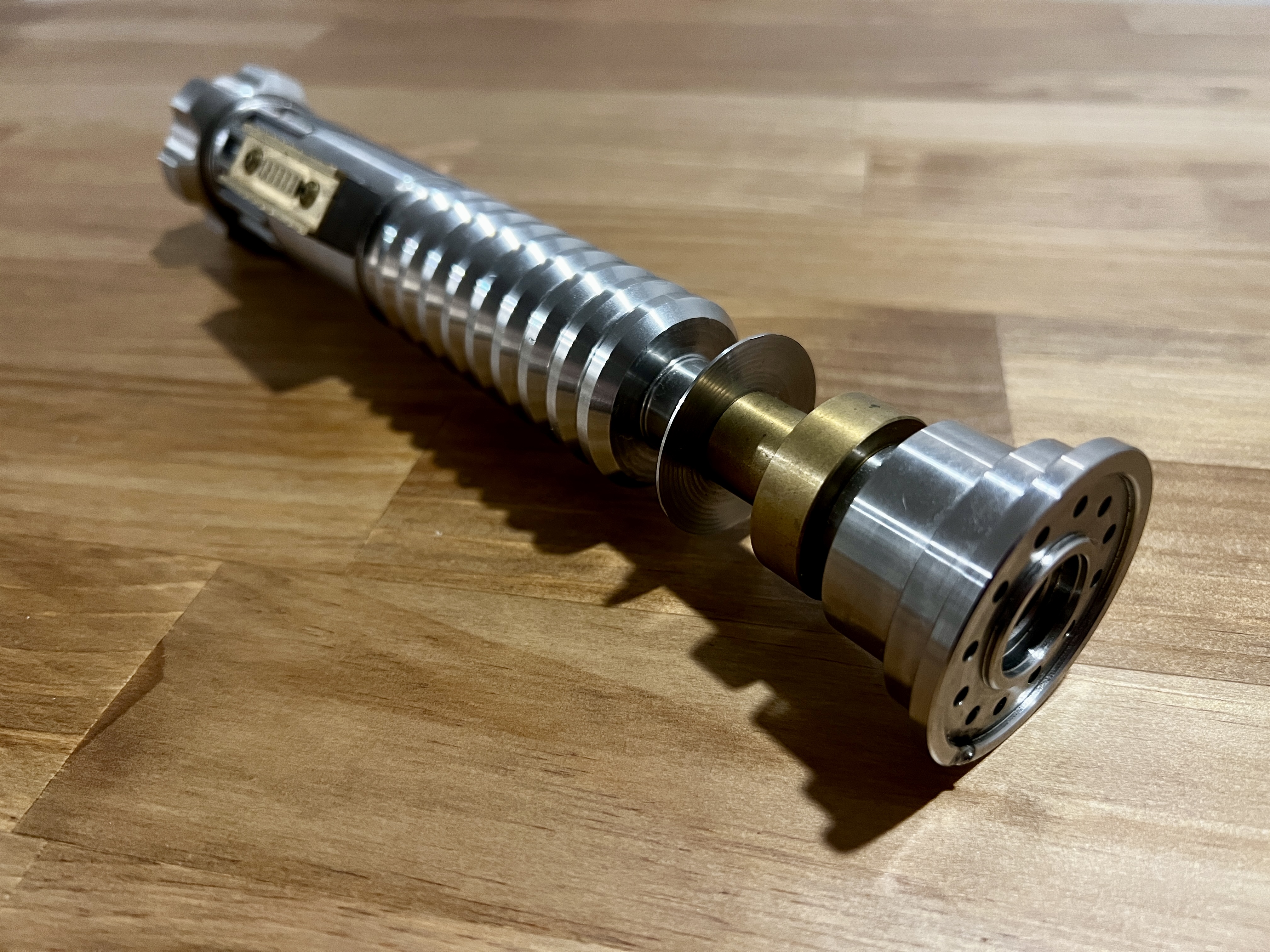
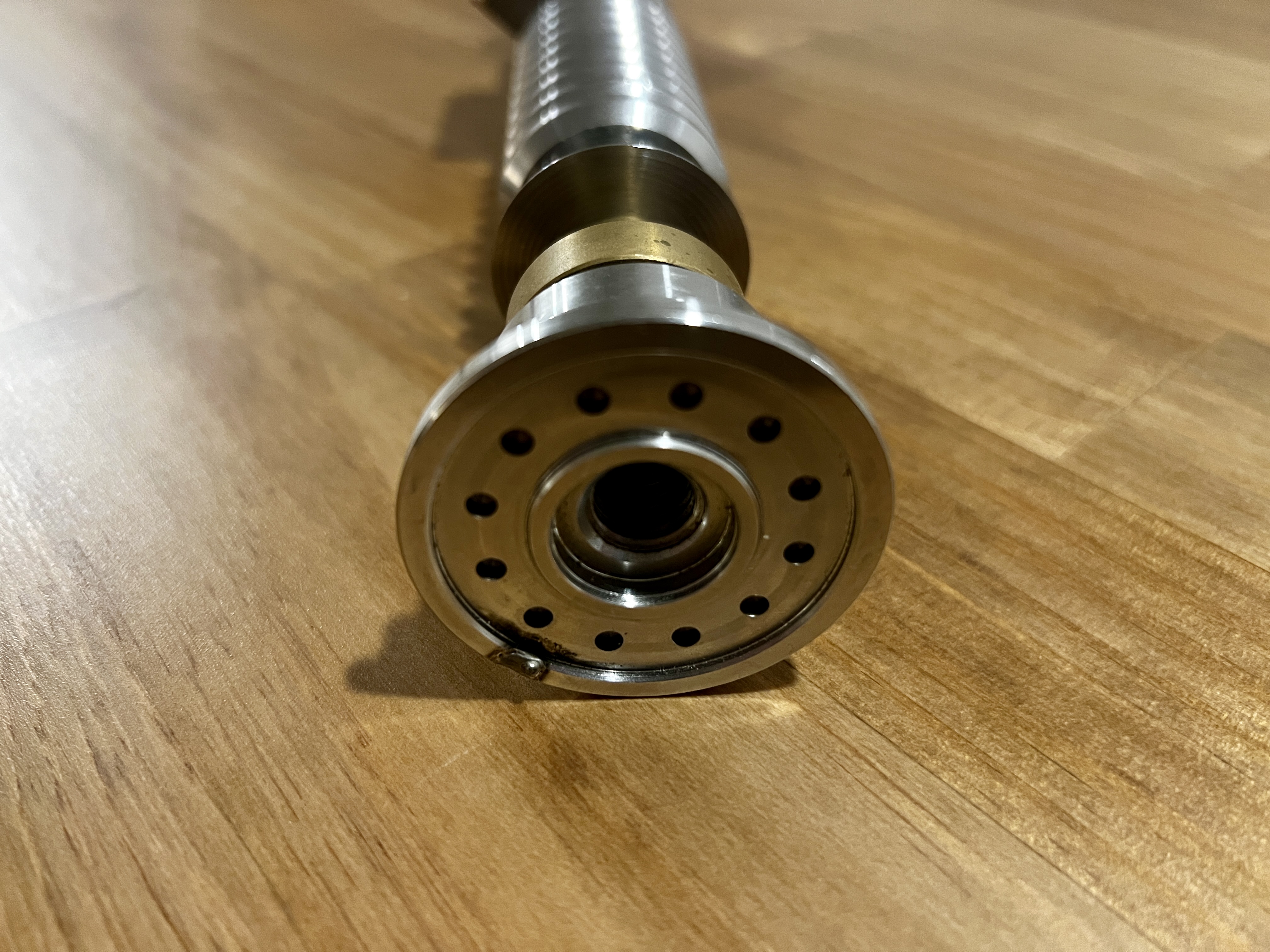
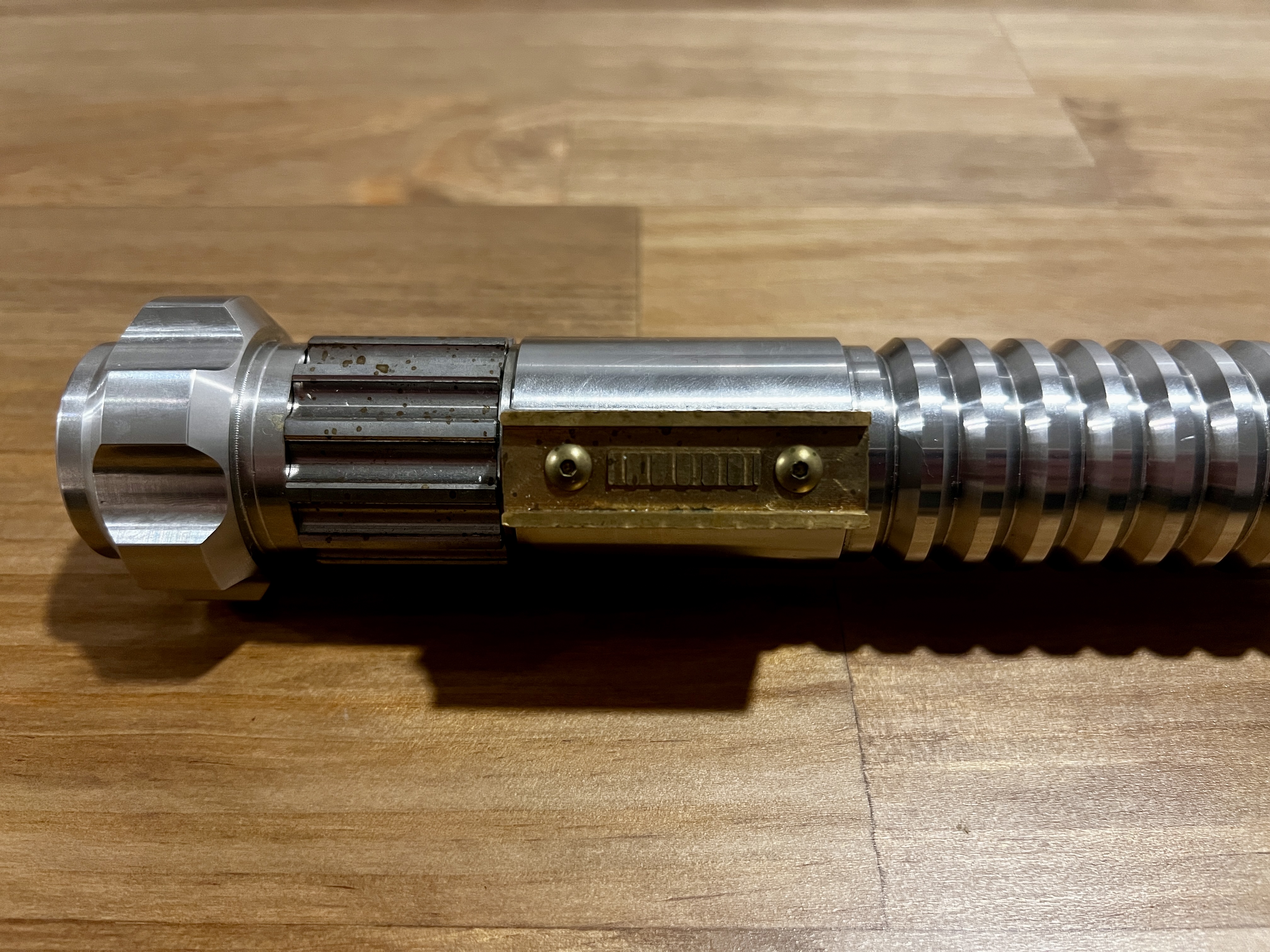
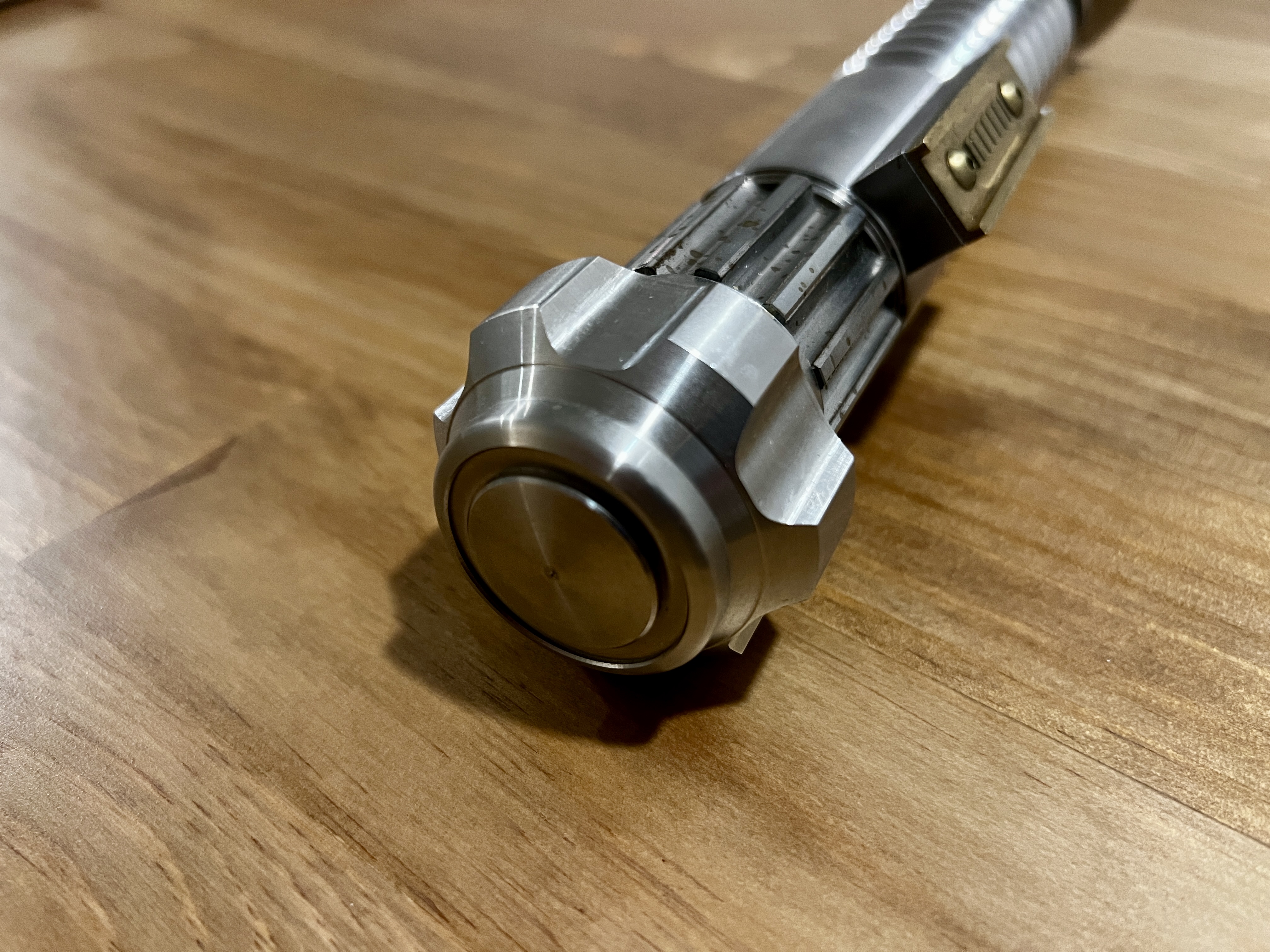
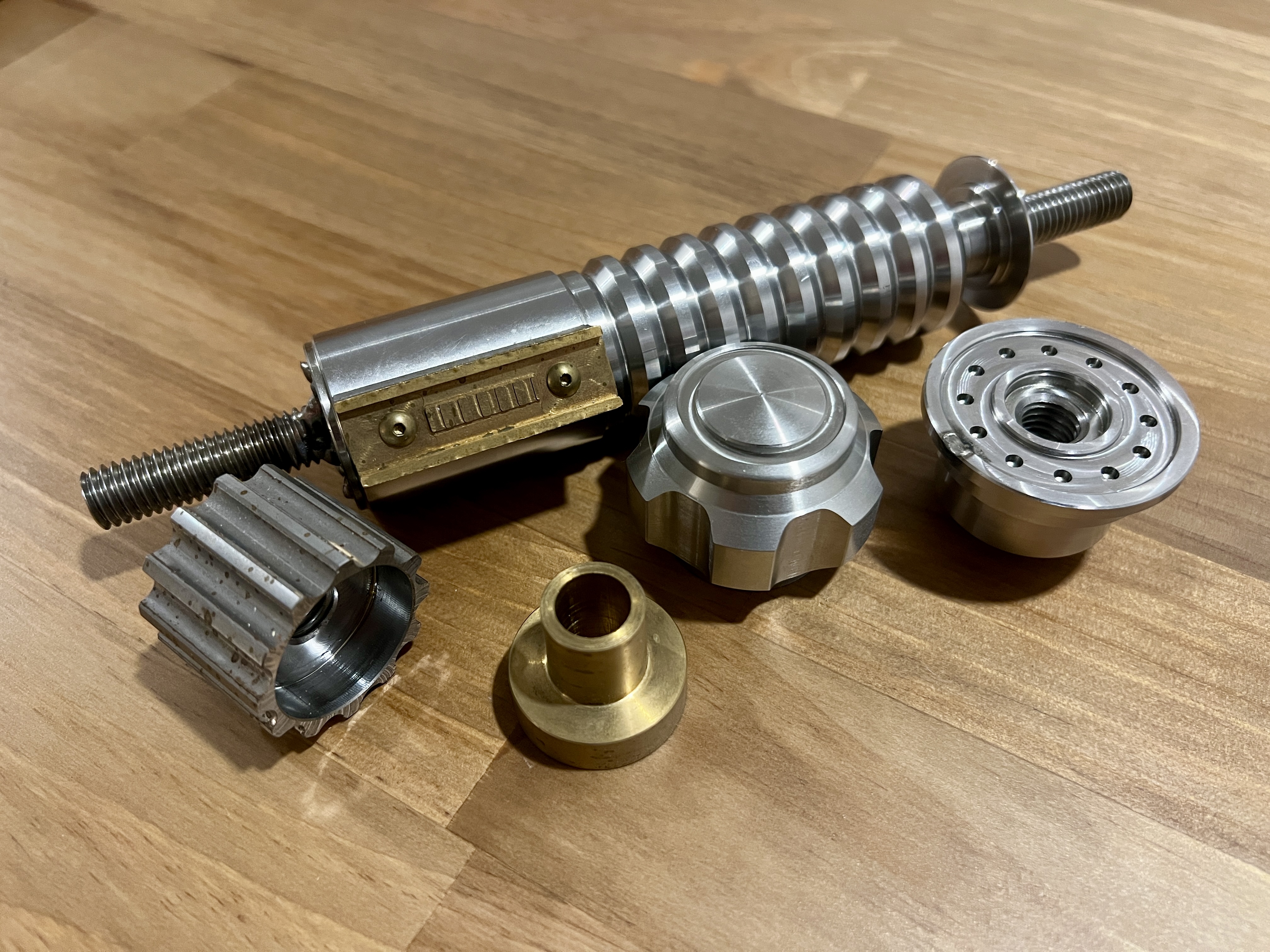
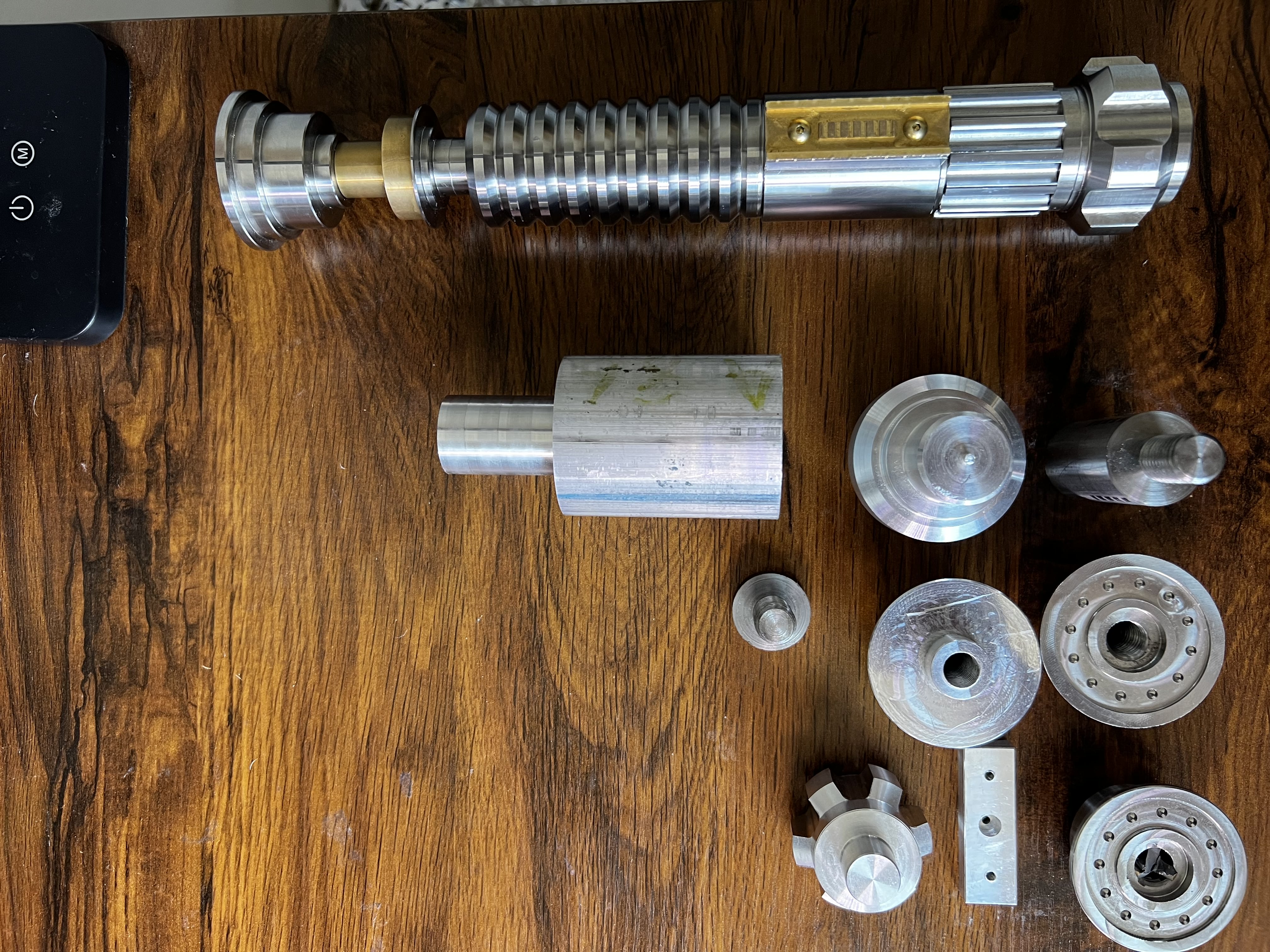
Overview
A passion project turned machining masterclass. I designed and machined a 7-piece lightsaber hilt from brass, stainless steel (SS316), and mild steel to sharpen my CNC lathe and mill skills. The project tested my problem-solving—leading to welding, heat treating, and material upgrades. After 50 hours of design, planning, and machining, it is now my living room's centerpiece.
Technical Details
- Components: 7 machined parts (brass, SS316, mild steel)
- Software: CAD and CAM in Fusion 360
- Machining Process: CNC lathe & CNC mill
- Heat Treatment: Self-taught heat treating process for durability
- Scrap Rate: 2 failed hilts before a final successful build
- Time Investment: 50+ hours
Development Process
- Design & Programming: Modeled in Fusion 360, generated toolpaths for CNC machining.
- Machining & Challenges: Cut and shaped components on CNC lathe and mill.
- Material Issue: Discovered galvanic corrosion on mild steel due to dissimilar metal contact.
- Solution: Upgraded all mild steel components to SS316 to eliminate corrosion.
- Learning & Repairs: Heat treated parts in my garage and welded a threaded rod after a tap broke.
Results
- Functional & Durable - Eliminated corrosion issues with full SS316 construction.
- Hands-On Learning - Improved machining, heat treating, and welding skills.
- Personal Achievement - A handcrafted centerpiece in my home decor.